Cold Stores – Achieving Growth Through Synchronisation

01 February 2016
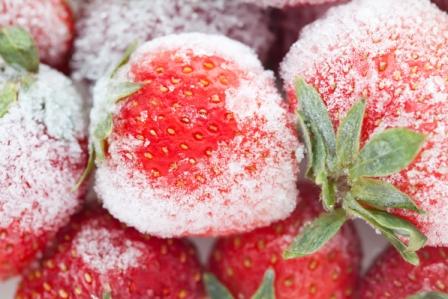
Cold stores are an essential piece of the supply chain puzzle, however, are they really that special? Whilst the controlled environment maintained and operated in is special, essentially it is the same operation as an ambient warehouse. They will still have to comply with tough regulations from the BRC alongside individual retailers pushing for their own snap audits, as well as more visibility and traceability than ever before.
It is not quite that black and white though, the controlled environment adds costs and frequently constrains normal warehouse operations. For example, employees have to wear special clothing and take frequent breaks. There is also a lack of operational flexibility, operators are significantly constrained in where they position additional storage or picking faces; unlike an ambient operation.
The “special” bit in operational logistics terms is metrics. Whether measured as cost per case, per order or per pick, costs are higher than ambient operations and any inefficiencies will be exacerbated. A logistics operation is the sum of its parts and to be successful these parts have to be synchronised. A cold store operation can be considered as five “parts”.
1. Storage / Capacity
The optimum storage system is one that provides a dense system in a small space, reducing the costs to build and operate. There are many racking systems available, ranging from very dense with direct access to “only the front pallets” to systems where every pallet is directly accessible.
In general, the fewer and the narrower the aisles, the more capacity there will be. Providing slot sizes to suit your products and pallets, whilst making sure that the right locations are used for the right product will maximise capacity.
However the utilisation and efficiency of a storage facility is not just the number of pallet spaces provided or occupied. If stock and movement profiles do not sync with storage and handling systems then extra cost and time will be built into the daily operation.
2. Operating Equipment
Like any warehouse operation there are many options, from fully automated crane and shuttle systems to manual operations with forklifts and picking trucks. An automated system can be used to shuffle pallets around, accessing the “pallet at the back” at little additional cost compared to a more manual solution. This can justify an automated solution by allowing more capacity without excessively increasing operating costs. This all takes time, so optimal processes and systems are key.
3. Processes
When looking at the processes in a fulfilment operation there are two main considerations to look at: How much time is available; what resources can be used.
There are a number of options from individual order picks, to multiple order picks, to a batch pick and outsort. Different methods might be best suited at different times of the day, at different periods of demand or seasons.
Picking is not the only consideration, inbound and put away as well as replenishment, “preparation for picking” and despatch also need to be reviewed. For example, if stock is being delayed at goods in or pickers being sent to empty locations due to late replenishments then this will slow down the whole operation. Many operations are limited in their choice of methods, or the set up and choice of locations by their systems.
4. Systems
A crucial part of operational efficiency is the warehouse management system (WMS). It is required to maintain the cold chain, provide evidence for the audit and support the operation. The WMS, whether it is a specialist piece of software or a module of an ERP system, requires suitable functionality for the operation. It should enable the operation to be as optimised as possible given its processes and equipment.
5. Hardware
Unlike ambient warehouses in a cold store the right hardware is vital. Whether it be a mobile device or voice solution the effectiveness will fall along with the temperature, unless a device is specifically designed for the conditions it is expected to perform in. It is vital that the hardware is enhanced to maintain efficiency in temperature controlled environments so it is able to reliably execute the tasks and processes dictated by the WMS. Malfunctioning devices can stop a warehouse in its tracks.
Cold storage is a changing industry and the potential for growth is strong. The operational logistics will be at the centre of any growth strategy. A strategy that achieves a sensible balance between capacity and efficiency, underpinned by technology, is the best way to meet the demands placed on the facility and turn opportunity into profit.