voestalpine Metsec select EPOD system from Manchester-based TouchStar Technologies

20 September 2023
Manchester, UK. 20th
September 2023: voestalpine Metsec select EPOD system from Manchester-based
TouchStar Technologies
Background
Voestalpine Metsec
plc is the UK’s largest specialist cold roll-forming company providing products
for the construction and manufacturing industries. The company focus is on
adding value through expert design, precision manufacturing and on-time in-full
product delivery.
The company’s origins
can be traced back to 1854. In that period, Oldbury in the West Midlands
became a major centre for the processing and fabrication of iron and steel
components. This “feel for the metal” lead the company Johnson & Kinder to
relocate their railway carriage company from Bromsgrove to Oldbury. From this
location they built the Birmingham, Wolverhampton and Stour Valley railway
line.
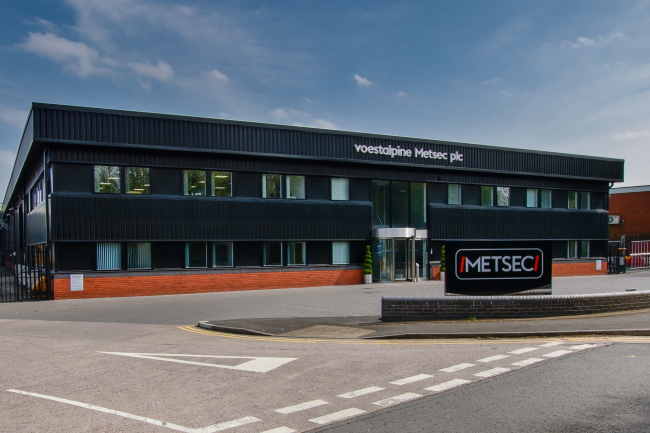
In the decades that followed the company saw many different
transformations, including an extensive period under the ownership of the Tube
Investments (TI) group and the formation of Metal Sections Ltd in 1945. Fast
forward to 1998 and the company was sold to an Austrian steel company,
voestalpine. This lead to some restructuring and the sale of some non-core
businesses but also enabled significant inward investment over the following
decades to keep Metsec in a market-leading position.
As a key
organisation within the €10 billion voestalpine group, Metsec has
continued to flourish and its range of purlin and framing systems have been
utilised within many of today’s landmark UK construction projects including The
Shard, Queensferry Crossing, Canary Wharf Crossrail Station, the Wimbledon
Centre Court roof as well as substantial international projects such as Nakilat
Damen ship yards (Qatar).
The Project
With its publicly declared focus on ‘on-time delivery’ the
company maintains a policy of continuous improvement regarding delivery
performance and is constantly refining, and investing in, new systems and
processes. This search for a ‘best of breed’ delivery and tracking system led
the Metsec management team to adopt the PODStar system from Manchester-based
TouchStar Technologies.
Metsec do not run their own
delivery vehicles but rather delivery work is carried out by 3rd
party hauliers. These hauliers equip their drivers with a variety of different
mobile devices and smart phones. With this in mind, one of the key system
requirements was to have a front-end application that ran equally well on both
android and iOS operating systems. The PODStar system is browser-based which
means that it is entirely ‘OS neutral’.
The
Cloud-based PODStar system offers a 'Planning and Optimisation' tool that automates
existing manual processes. Using real time job information, clients are
able to drag and drop jobs onto the relevant vehicles. The PODStar system has
been fully integrated with Metsec’s existing sales order processing systems,
via XML file transfer. Once a manifest has been created it is then
automatically sent out to the drivers remotely in the field. To further enhance
the efficiency, via a click of a button, jobs are automatically allocated
vehicles in the most efficient order and display the route on a map
saving Metsec fuel and time on the road.
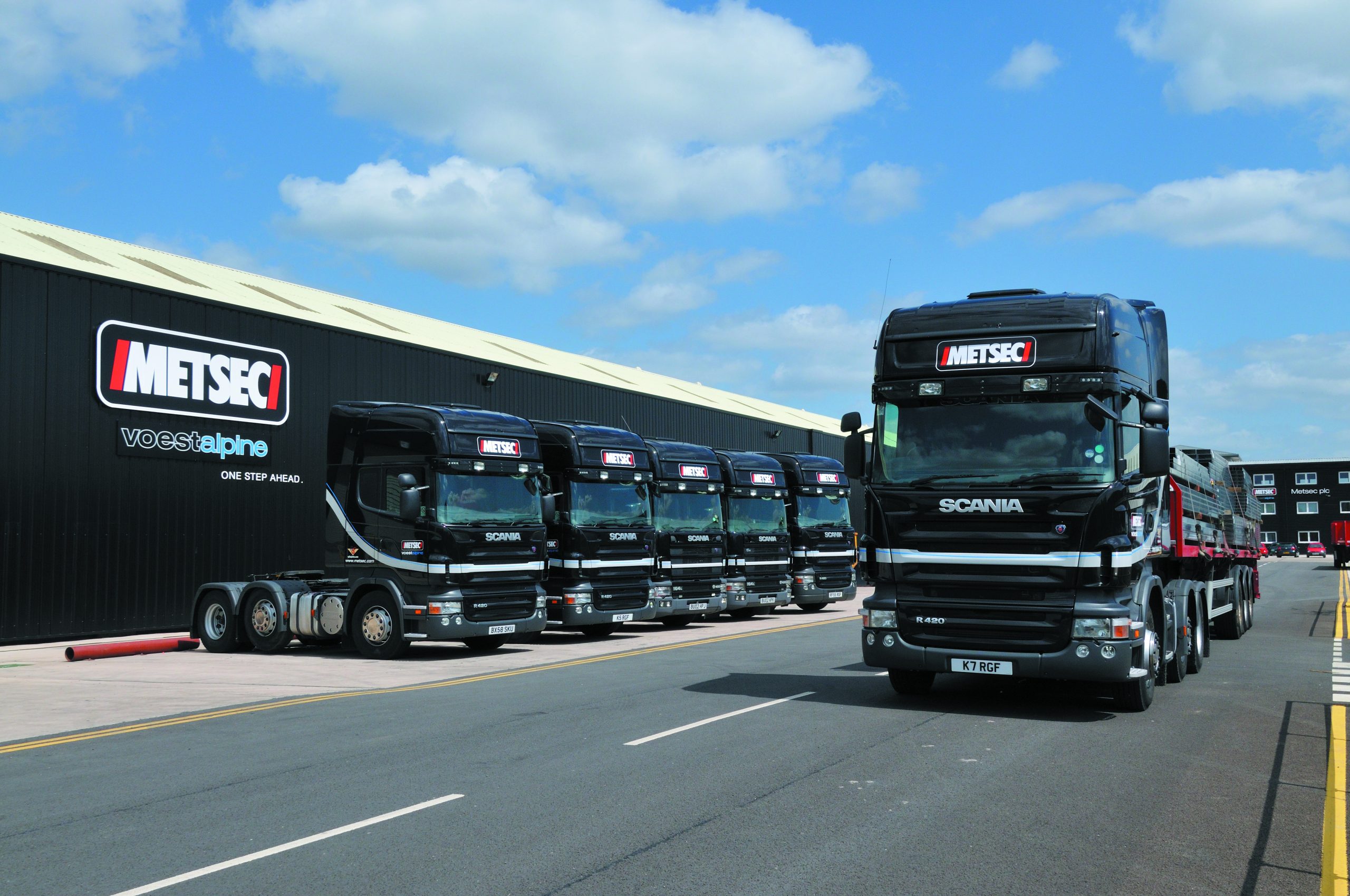
Once downloaded the driver
can receive their jobs and complete in real time. Metsec delivery drivers are
equipped with smart phones with the handheld device used for both proof of
delivery / signature capture and tracking of the driver and vehicle location.
Back at the Metsec headquarters, management can view a real-time
update on a map showing the fleet position as well as additional data and
the job status and driver performance.
Touchstar
are constantly enhancing the PODStar software functionality and Metsec make
heavy use of the system’s latest ‘waiting time’ feature. This field is
contained within the system’s job status web page and enables management to
specify an anticipated waiting time for a job and to determine, in real-time,
when this has been exceeded. This information can be useful to resolve dispute
scenarios where a driver has met his allocated delivery slot but is made to
wait unnecessarily by the client.
With
regard to their vehicle fleet, Metsec take their responsibilities in the area
of employee and public safety very seriously. Drivers are using their
smartphones to carry out their daily vehicle checks. In the event of a
discrepancy being recorded the driver is forced by PODstar to take a photo of
the defect and record notes. All
defected items are immediately emailed to the depot transport manager and fleet
engineer ensuring that remedial work is scheduled without delay.
The
Outcome
Ian
Hemsley (Metsec Production Director) comments: " We
have the PODStar system installed in four of our divisions. In TouchStar we’re
happy that we’ve found an organisation whose professionalism extends beyond the
product itself, right through to the installation and support aspects of the
project. Our drivers appreciate the simplicity and user-friendliness of the
system and it has also ensured that we're legally compliant. Overall we're
delighted with the system and, as we continue to expand, we look forward
to a long-term relationship with TouchStar."
To
discover more about voestalpine Metsec please visit http://www.metsec.com/.
Press
Contact:
Mike
Turner
Group
Marketing Manager
Touchstar
Technologies
Mike.turner@touchstar.co.uk